Nabors has launched its latest autodriller upgrade, featuring enhanced logic and precise Weight on Bit (WOB) and differential pressure control. These improvements drive higher rates of penetration (ROP) while significantly reducing bit wear and minimizing drilling dysfunction, empowering operators to achieve more efficient and cost-effective operations.
Unlike traditional autodriller systems, Nabors’ autodriller requires minimal input from drillers, automatically maintaining target parameters without overshooting and ensuring consistent slack-off rates. By seamlessly automating these processes, it allows drillers to focus on broader surface drilling parameter optimization, operational goals and maximizing the overall productivity of each well.
Designed to be rig agnostic, the autodriller integrates with Nabors’ control system on any rig. For operators using Nabors rigs, this solution is included, providing the full benefit of the autodriller’s capabilities without additional costs.
Key Features and Benefits
- Precise WOB and differential pressure control for optimized drilling performance
- Enhanced ROP
- Reduced bit wear
- Less driller intervention, enabling focus on surface parameter optimization
Proven Results from the Permian Basin
The latest autodriller upgrade has already delivered significant results in collaboration with a major operator in the Permian Basin:
- Lowest Bit Wear Across Contractors: Delivered the lowest bit wear and the fewest runs among all contractors during field testing.
- Increase in Rotary ROP: Achieved a 22% improvement in rotary ROP, while maintaining consistent WOB and improving control by 63%.
- Collaborative Development: Built in collaboration with a leading Permian operator, ensuring the technology meets real-world demands and enhances performance.
Through this upgrade, Nabors continues to lead the way in drilling automation, delivering smarter, more efficient solutions. With its next-generation autodriller, Nabors is setting a new standard for precision, control, and value.
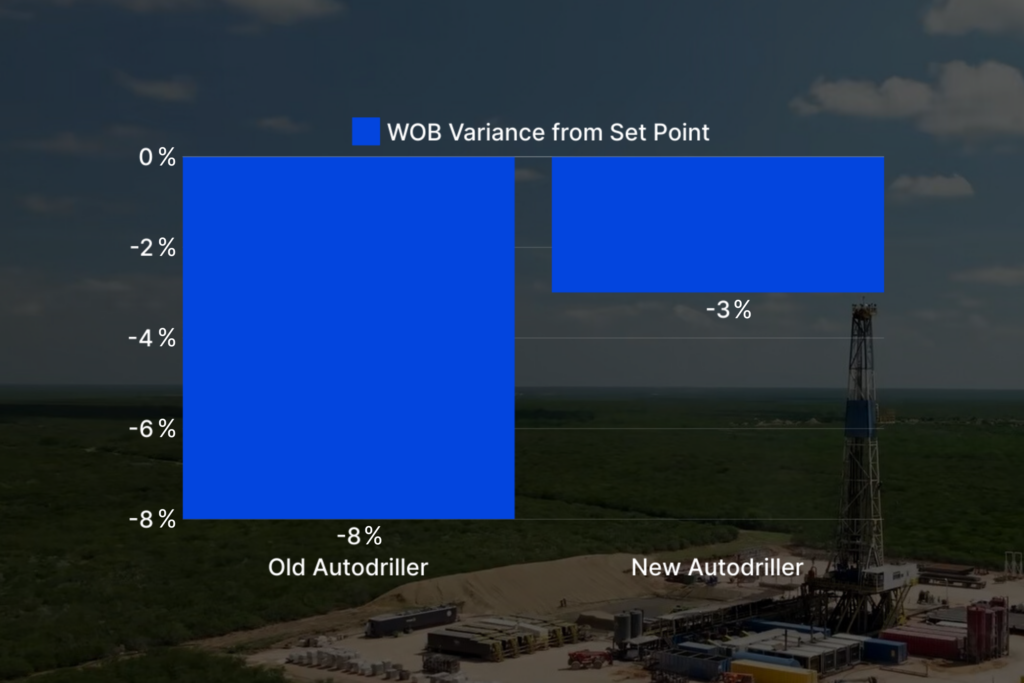
This graph is showing the weight on bit variance from set point with a 63% improvement comparing the old vs new autodriller for a major operator in Texas.